NC旋盤を目指している方は、この絵の部品を加工する工程がイメージできますか?
(ヘタな絵ですみません)
この記事では、歯車になる前の段階の部品『ギアブランク』をNC旋盤を使い、加工する時の方法を紹介します。
- 厚さ 5㎜
- 外径 Φ15.8㎜
- 内径 Φ6㎜
- 材料は 金属 とします
この部品の外周にギザギザ(歯車の歯)を削って、最終的に『ギア』になります。
ほんの一例ですが、これからNC旋盤を始めようと思っている方は、参考にしてもらえたら嬉しいです。
上記の図面の場合、経験者でしたら瞬時に加工方法がイメージ出来ると思いますが、これからNC旋盤の道へ行こうとしている方でしたら、まず、加工方法は分からないと思います。
また、加工方法も1つではなく、何通りもあります。
そんな中で今回は一番オーソドックスな方法を紹介していきます。
- 機械は正面主軸と背面主軸の2つを装備している機械を元に説明していきます。
※ブランクとは、一般的に空白という意味だったりしますが、製造業では最終的な製品になる前段階の製品のことをブランクと呼んだりします。なので、今回はギアになる前段階の製品なので、ギアブランクと呼びます。
NC旋盤加工で大事なポイント
先ほどの図面の中で、寸法に公差が入っているところが3つありました。
上記赤枠で囲ったところです。
NC旋盤という量産品を扱う業界では、100個や1000個、10000個であってもこの寸法精度はクリアしてなければなりません。
しかし、金属の材料をひたすら削り続けていくと、削っている刃物も摩耗してきて、寸法が変わってきてしまいます。
その為、定期的に寸法確認をしながら、すこしづつ刃物補正を入れていきます。
赤枠で囲った以外のところは、一般的には±0.1㎜までは許容範囲としますので、C面取りについては、多少の誤差が出ても寸法公差内(±0.1)でしたら、NGになることはないので、今回は省きます。
そこで、NC旋盤加工で注意しておきたいポイントは、
赤く囲った3か所の寸法を
しなければなりません。
ここを踏まえたうえで、加工工程を考えていく必要があります。
その為に、まずは
- 図面の中で注意すべき寸法にチェックを入れる
これは、NC旋盤の加工プログラムを考える上で、非常に重要です。そして、NCプログラムでなくても、機械加工では寸法公差の入っているところは特に気にするようにしましょう。
NC旋盤の加工工程を考えよう!
こちらもヘタな絵ですが、私なりに考えた加工工程図です。
旋盤加工の経験が無い方にとっては、「?」だと思います。
簡単に説明すると、
- ①②で表面(右側面)を削ります
- ③④⑤⑥で穴と穴のC面を削ります
- ⑦で右側外周のC面と外径を削ります
- ⑧で材料から切り離します
- ⑨で左側外周のC面と裏面(左側面)を削ります。
- ⑩でC面を付けます
すごく簡単な形状ですが、これだけの工程が必要になってきます。
また、量産部品加工では1秒でも早めることが利益率をあげられますので、例えば加工サイクルを早める為には、6つの工程を5つしたりすることあります。
しかし今回は、加工方法を切り詰める(時間短縮させる)内容については、軽く触れる程度にしておきますね!
後ほど、それぞれの工程について説明します。
NC旋盤の加工イメージできたら次は刃物を決めよう!
ここまでが、右側からの加工で必要な刃物です。
そして、こちら↓は左側の加工で必要な刃物です。
NC旋盤加工の場合、加工の流れ(加工工程図)と使用する刃物が決まれば、もう加工プログラムも出来た様なものです。
あとは、自分で思い描いたイメージに沿って、GコードやMコードで書いていくだけです。
また、対話式のNC旋盤機では順番に画面の指示に沿って、選択して行くだけなので、Gコードが覚えられない!ということも無く、加工プログラムは出来てしまいます。
※初めは対話式よりも、手打ちのプログラムで慣れて言った方が応用が聞きます。ただ、いきなりNC機械に向かって打ち込むよりは、一度ノートに下書きするのが現実的です。紙の上で一度や二度見直してから、機械に打ち込んでいった方が、ミスが減るのと機械を止めている時間が少なく済みます。
NC旋盤加工の手順
NC旋盤では、まず初めに行う加工
ツラナメ が非常に重要だと私は感じてます。
理由は、ツラナメした面が製品寸法全ての基準になるからです。
では、さっそく説明してきますね!
材料の端面の切り落とし
まずは鉄の棒の端面を一度切り落とします。
切り落とすことを旋盤用語では、
突っ切る ⇒ ツッキリ
と呼びます。
NC旋盤で使う材料(一般的に約2m~2.5m)で外径が研磨された材料以外は、両端面は大きなC面が付いていたり、引き抜き材の場合、寸法が少し細くなっているからです。
そこで初めに使う刃物は
①のツッキリです。
ツッキリの刃物番号を『T1』としました。
※刃物番号(刃物の名前や番地のようなもの)はプログラムを作る時に刃物を呼び出す為に必要ですが、始めは「そうなんだー」くらいに思ってて大丈夫です。
大切なのは、加工の流れを把握することです!
先端を50㎜くらい切り落としたら、次はその端面を綺麗に整えます。
この整えるのが、
②ツラナメです。
ツッキリという刃物は材料を切断する刃物なので、切断面はあまり綺麗ではありません。その為、ツラナメという刃物(超鋼チップ)で、表面を一皮(0.1㎜程度)加工します。
この時、ツラナメする時の刃物を『T2』にしました。
これで、製品加工をする基準面が整いました。
※ここまでで、ツール番号は『T1、T2』の2種類です。
中心に穴を開ける
製品端面が整いましたら、次は真ん中に穴を明けます。
いきなりドリルで開けると、穴が曲がってしまったり、中心がズレてしまうことがありますので、まずは『センタードリル』というもので、中心に少し凹みを付けます。
センタードリルとは↓これです。
いわゆる、センターポンチみたいな使い方をするものです。
深さは、先端の細いところだけで構いません。
深さにすると1~2㎜程度です。
この刃物が ③センタードリル です。
このセンタードリルを『T3』という工具名(ツール番号)にしました。
センタードリルの後は、Φ6の穴径に対して少し小さめのドリルで穴を開けます。私の場合は、Φ5.9㎜のドリルを使用します。
↑穴開けように用いる普通のドリル
★この穴は、寸法公差が(0~+0.01)と厳しいので、このあとで使う『ザグリバイト』というもので、ビシッ!と決めるので、やや小さめのドリル径を使います。
ところが、あまり小さすぎるドリル(Φ5以下)を使ってしまうと、ザグリバイトによる削り量と負荷が増えてしまい、寸法精度が暴れてしまう可能性と、バイトの摩耗も早くなってしまいます。
そのため、直径で0.1㎜、片側0.05㎜の残り代(削り代)狙いにします。
※Φ5.9㎜のドリルで穴をあけると、実際は5.9㎜よりやや小さくなりますが、キリコ(削りカス)が絡んでくると、太く(Φ5.95など)なってしまうので、キリコが絡まない絶妙な角度で切削油がかかるようにしましょう!
使用する刃物は ④Φ5.9ドリル で、この刃物を『T4』というツール番号にしました。
ドリルでΦ5.9㎜の穴を開けたら、次は穴の入口のところにC面を付けます。今回は、90°のセンタードリルで軽く当てて、C面を付けます。
センタードリルがこれ↓です。
また、穴の直径が6㎜なので、Φ6以上でなければC面が付けられませ。その為、センターはΦ8㎜の物を使いましょう。
⑤90°センタードリル
この刃物を『T5』とします。
C面が付いたら、いよいよ寸法公差の厳しい
Φ6㎜公差は+0.01~0 です。
この寸法公差を保つためには、ザグリバイトという刃物で一皮削るようなイメージで寸法を整えます。
ザグリバイトは、手作り製のものでも構いませんが、今回は特殊な形状ではないので、刃先が摩耗してきたらチップ交換がすぐに出来る超鋼チップ製バイトの方がお勧めですね!
このような物↓
ということで、
⑥ザグリバイト を『T6』とします。
穴があいたら、次は外径を削ります。
外径を削り寸法を整える
続いては、外径のΦ15.8㎜(寸法公差0~-0.03)を削っていきます。
ここで使う刃物は、先ほどツラナメをした時の刃物と同じ形状のもので構いません。しかし、あえて先ほどとは違う刃物をもう一つ使います。
※寸法補正?と疑問に思っても、NC旋盤業で1週間も働いてれば、ほとんどのところで補正の入れ方は教えてくれますので、安心してください。
ということで、⑦外径
この時のツール番号は『T7』としました。
製品の切り落とし
ここまでできたら、材料はこのようになっていると思います。
- 右側面
- 穴と穴のC面
- 外径と右側のC面
までの加工がおわりました!
あと少しです。
ここまで出来たら、次は製品を材料(長い金属棒)から切り離します。
この時は、始めに使った刃物 ①ツッキリ を再び使用します。
ツッキリは、製品の寸法を揃える為に使用する刃物ではないので、同じ刃物で構いません。
初めに材料の先端を切り落とした時と同じようなイメージです。
⑧ツッキリ 『T1』
ただし、この時ただ単に切り落としてしまうと、まだ加工途中の品物はNC機械の中へ落ちてしまいます。
そうならない為に、正面主軸と背面主軸を同期させてつかみにいく。
という動作をさせるのですが、それはプログラムのコードで指示をすることが出来ます。
今回は詳しいプログラムコードについては触れません。
左側面のツラナメ
残りは2工程です。
今回は、背面側の主軸があるタイプでの加工法なので、今度は製品は右側にいどうしてきました。
この時、製品の左側端面はツッキリで突っ切っただけなので、製品と言えるような綺麗な面ではありません。
その為、一番初めに行ったツラナメと同じ加工を左側面にも加工します。
この時の削り代も、0.1㎜くらいにしておくと良いでしょう。
0.2㎜では?削り代が多く刃物の痛みも早いから。逆に0.05㎜の方がもっと良いのでは?と感じますが、これは良くありません。
先ほど、刃物の補正を入れる。という項目があったと思いますが、機械をセットして、1日、2日、1週間と削り続けていくと、補正を入れていく量が積み重なり0.05㎜を越えてしまうこともあります。
すると、結果的に左側面のツラナメがされなくなってしまう。
もしくは、製品の厚みが薄くなったり厚くなってしまったりしてしまう。など寸法管理が難しくなってしまいます。
そうなってしまうと、一番初めに機械段取り(機械セット)した人か、ある程度分かる人が、1つ1つの刃物位置の状態を確認し直さないと良い製品は生み出されなくなってしまいます。
そのような理由から、0.1㎜を基準に左側のツラナメする
と覚えておきましょう!
⑨左側のツラナメ 『T30』とします。
あれ?なんで一気にTが30へ飛んだの?と、気になりますが、これは背面側の主軸工具(刃物)と正面側の主軸工具(刃物)とを分かりやすくする為です。
仮にT50でも何の問題もありません。
左側穴のC面取り
いよいよ最後の工程です。
左側の穴の入口にC面取り加工を行います。
これは、右側穴の入口に付けた時のC面と考え方は全く同じです。
90°のセンタードリル↑を軽く押し当てるだけです。
ただし、こちらは左側なので、旋盤の機械には、先ほどとは180°反対向きに全く同じものをもう1本セットします。
⑩センタードリル 『T31』とします。
あとは、製品を吐き出して(取り出して)完成です!
お疲れさまでした♪
★あわせて読みたいオススメ記事★
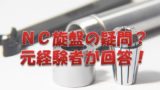
NC旋盤の加工工程をまとめると
NC旋盤の基本的で、オーソドックスな加工方法を紹介してきました。
これからNC旋盤の道へ行くのでしたら、一回くらいは読んでもらえると、実際に作業を経験していく中で、少しくらいは役に立つと思いますよ。
ちなみに、旋盤業へ転職・就職しようとしている人の中には、プログラムが覚えられるか心配です。
といった不安は尽きないようですね!
でも、安心してください(^^)/
私も、現役で旋盤工だった時は、簡単な形状の加工プログラムはそらで打ち込んでいましたが、旋盤屋から転職して早5年。
もうほとんど覚えていません。
加工プログラムなんて、その程度です。
しかし、今回紹介したように加工方法については頭と身体に染みついてますので、自転車の乗り方が忘れられないように、加工方法も忘れてません。
旋盤に限らず、製造業では
- いかに加工方法を身に付けるか
- よりたくさんの加工方法を知っているか
- 斬新な加工方法を考えられるか
その方がよっぽども価値がある人材だと私は感じてます。
たとえハイテクなCAD/CAMを使っても、根本的な考え方が分かってないと応用は利きません。
私も数種類の3D-CADは現在も使ってますが、そんな操作方法よりも3Dを画面上で作り上げていくイメージ(製作工程)の方がとっても大切だと思います。
ジジイくさいことを最後に書いてしまいましたが、お役に立てれば幸いです。
こんな記事もNC旋盤へ目指している人達に人気ですので、合わせて如何でしょうか?
コメントをどうぞ